You are in preview mode
De-carbonising Ammonia: alternatives to the Haber Bosch process?
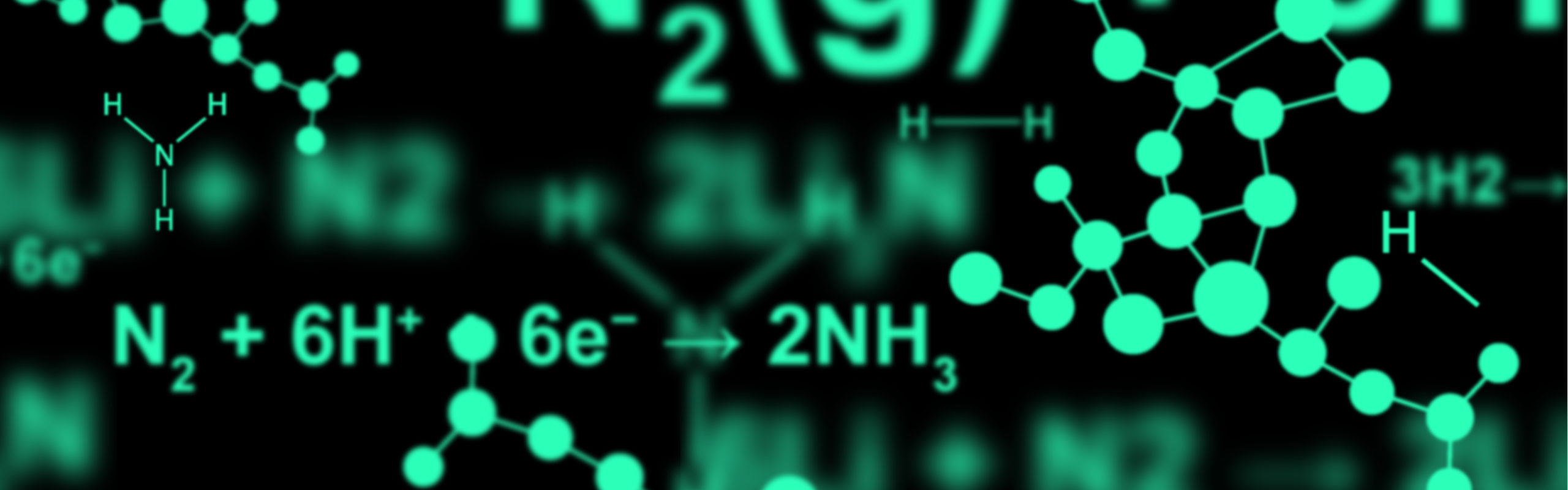
Throughout the 19th century the demand for nitrates and ammonia for use as fertilizers and industrial feedstock rose steadily. A principal source of nitrate was the droppings of sea birds (guano) found in the arid Atacama Desert in Chile but it was believed that these natural reserves could not satisfy future demand and so research into new potential sources of ammonia became more important.
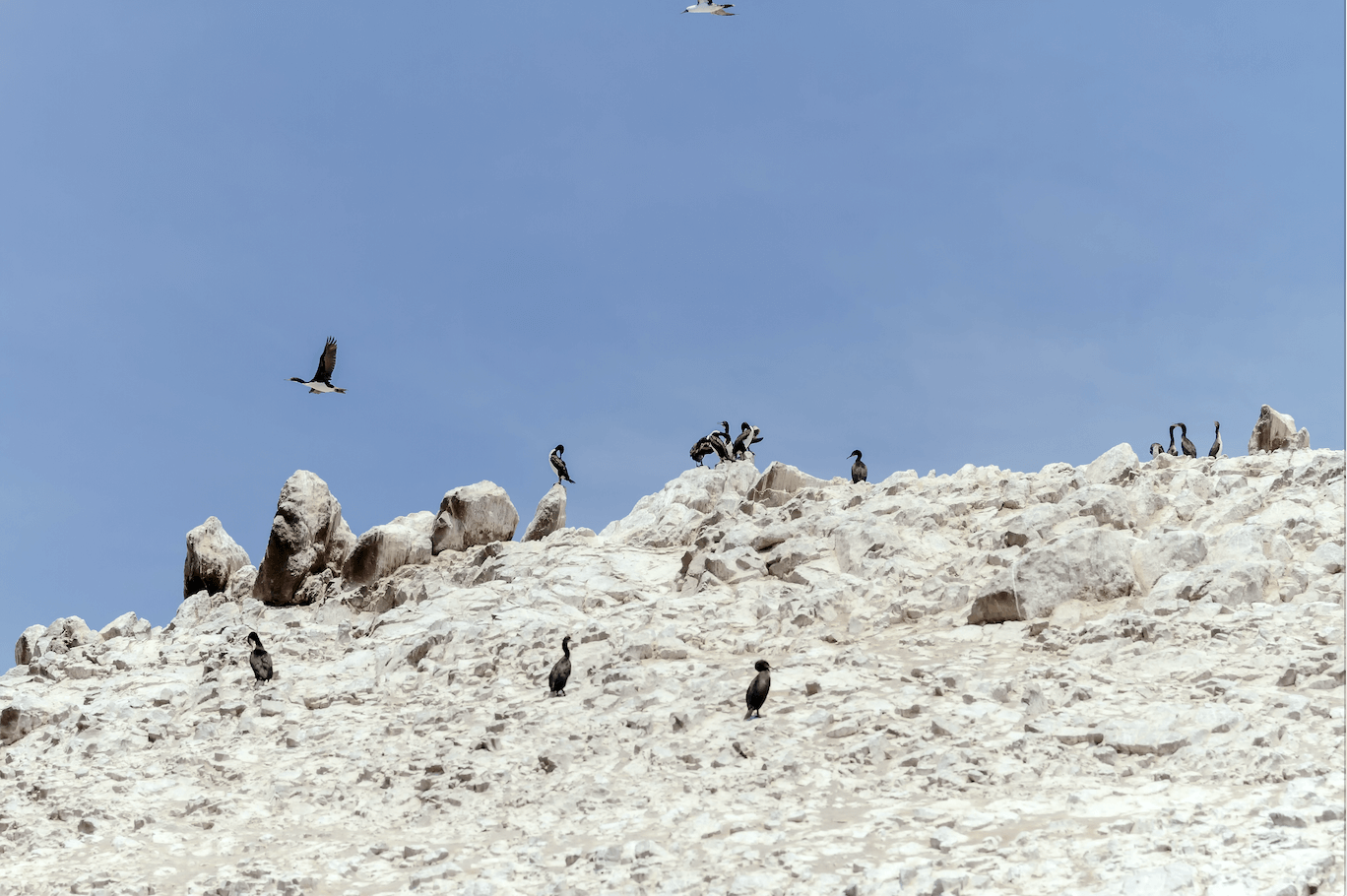
^ Cormorant birds on the guano in one of the Ballestas Islands (Paracas, Peru)
An obvious source of nitrogen (N2) was the Earth’s atmosphere. However, nitrogen is exceptionally stable: it will not react readily with other substances so the production of ammonia directly from nitrogen represented a serious challenge. Fritz Haber studied the effects of pressure, temperature and catalysts on the process in the laboratory in 1909. Carl Bosch, an employee of the German chemical company, Badische Anilin und Soda Fabrik (BASF), was given the task of scaling up Haber’s reaction many-times-over to industrial level which resulted in BASF manufacturing ammonia in 1913. Haber and Bosch were later awarded Nobel prizes for their work in overcoming the chemical and engineering problems involved.
The Haber Bosch process involves the reaction of nitrogen and hydrogen into ammonia at high temperature (500 degrees C) and pressure (200 atmospheres) in a reversible reaction.
N2(g) + 3H2(g) = 2NH3(g)
Fritz Haber realised that the speed of the forward reaction depended largely upon the fact that the triple covalent bond in nitrogen is really hard to break. He experimented by externally applying pressure and temperature to the dynamic equilibrium and also discovered that iron could act as a catalyst to allow the reaction to occur much more quickly.
Although the Haber Bosch process represented a huge technological advancement, its energy demands result in a massive carbon footprint. Hydrogen used in the process comes from methane (CH4) obtained from fossil fuels (natural gas, coal and oil) through processes that release CO2. From hydrocarbon feedstock through to NH3 synthesis, it is estimated that every NH3 molecule generated releases one molecule of CO2. Since modern agriculture depends on nitrate fertilizers based on ammonia, a significant part of our food is effectively a product derived unsustainably from fossil fuels. The Haber Bosch process is over 100 years old and is expensive in energy consumption but no industrial-scale alternative exists and so it remains in use today. High emissions of the potent greenhouse gas, carbon dioxide, provide strong impetus for modern research effort into other processes which may use sources of green electricity.
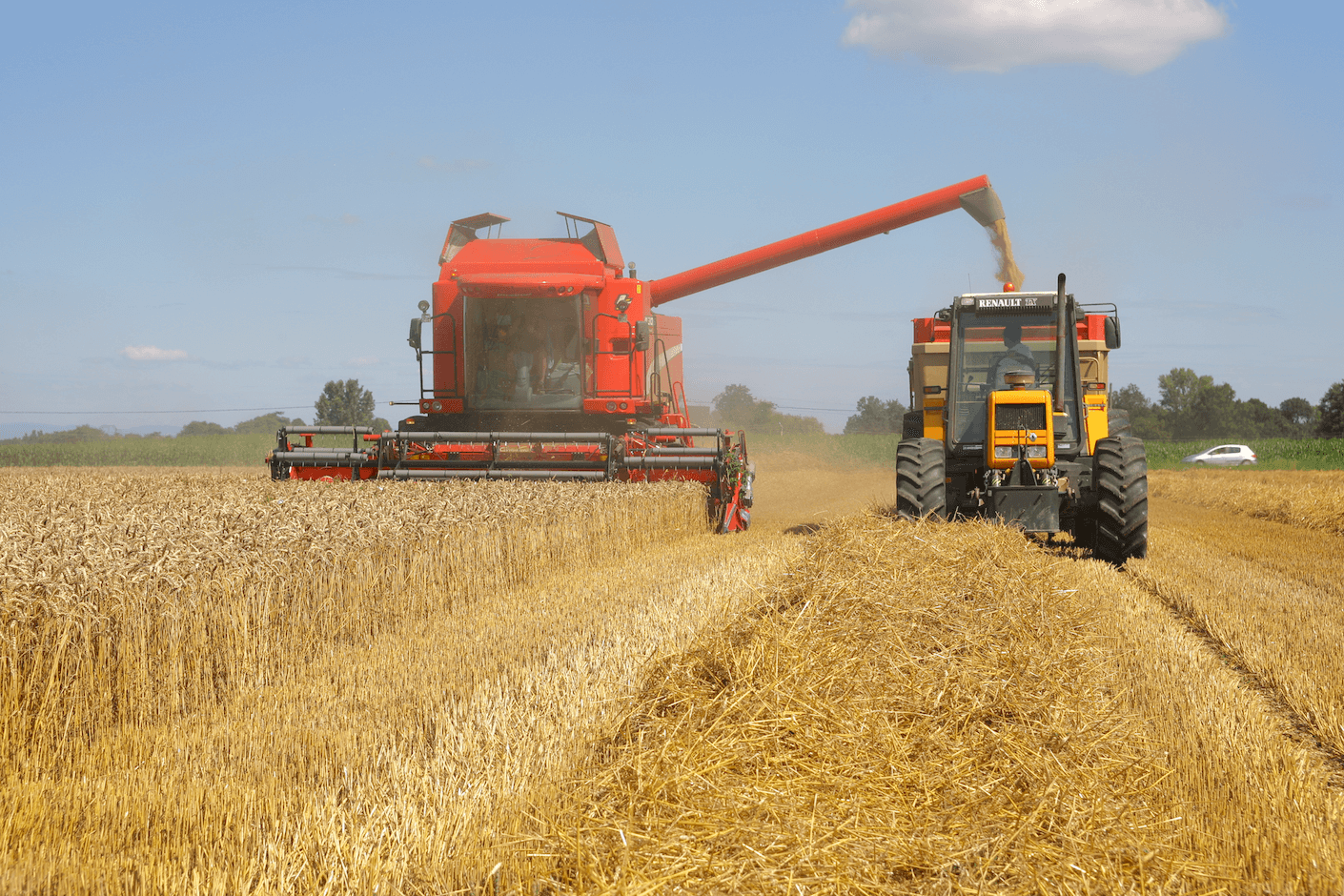
^ Wheat Harvest
In the past ten years or so, the increasing availability of low cost, renewable electricity has encouraged research into alternative approaches involving electrochemical technologies. In the United Kingdom and in many other developed nations too, electricity is generated from a number of different fuel sources avoiding reliance on one source so that constant supply of electricity can be maintained. Supply of electricity to the national grid still depends upon burning fossil fuels; natural gas (35.4%), coal (0.5%) and oil (3%); renewable sources accounted for 47% with the balance from nuclear fission reactors. Renewable technologies use natural energy sources such as wind, wave, tidal, hydro, solar, geothermal and bio-mass (Department of Business, Energy & Industrial Strategy).
The Siemens Green Ammonia Demonstrator at the Rutherford Appleton Laboratory in Oxfordshire goes part of the way along the road to producing ‘green’ ammonia in that hydrogen is produced by electrolysing water and nitrogen is extracted from the air. The conventional Haber Bosch process then produces ammonia.
Over the past two decades, other alternatives to the existing Haber Bosch process have been investigated among them direct electrochemical synthesis. Research has been carried out in aqueous, molten salt and solid state electrolytic cells. Ammonia has been made from its elements at atmospheric pressure in a solid state electrochemical cell. Gaseous H2 and N2 were introduced over the anode and cathode, respectively. At the anode, H2 was converted into protons, which were electrochemically transferred to the cathode where they reacted with N2 to produce NH3:
Anode: 3H2 → 6H+ + 6e−
Cathode: N2 + 6H+ + 6e− → 2NH3
Overall: N2 + 3H2 ⇄ 2NH3
Direct production of ammonia in an electrochemical cell has so far been inconclusive. There is a tendency for atomic hydrogen (H) or hydrogen ions (H+) to reform molecular hydrogen (H2) quickly rather than combine with free nitrogen atoms to produce ammonia (Marnellos G. 1998 and Garagounis I., et al 2019).
A process definitely known to produce ammonia was first reported in Japan during the 1990s and involves lithium nitride. Lithium is the smallest and most reactive atom of the Group 1 alkali metals. Lithium reacts exothermically with nitrogen gas at room temperature forming crystalline lithium nitride (Li3N).
Lithium will even react readily with nitrogen in the air to give lithium nitride.
6Li + N2 → 2Li3N
Lithium nitride is a stable reddish-pink crystalline solid which reacts violently with water to produce ammonia:
Li3N + 3H2O → 3LiOH + NH3
While much hope has been vested in electrochemistry as a possible solution, the current efficiency of such processes is typically below 1%. However, scientists at Stanford University in California have recently devised a cyclic, electrochemical process to make ammonia involving lithium nitride and report an efficiency of 88.5% in the laboratory. Electricity from a renewable source is used electrolyse lithium hydroxide and produce lithium metal. Exposing this lithium to a stream of nitrogen gives lithium nitride. Lithium nitride is then hydrolysed to produce ammonia and regenerated lithium hydroxide. The process works at ambient pressure, moderate temperature and importantly does not require the expensive production of hydrogen (J M McEnaney, et al. 2017).
Research continues into the properties of cheaper metal nitrides, such as magnesium nitride (Mg3N2), which can produce ammonia in a similar way. Other investigations examine the use of metal nitrides acting as catalysts to produce ammonia directly from its constituent elements. However, means have not yet been found to scale-up any of these reactions into an industrial process capable of replacing the Haber Bosch method and meet the huge world-wide demand for ammonia.
One of the greatest challenges of the present day is de-carbonization of the global economy and finding an alternative to the Haber Bosch process would certainly help. An important contribution is being made through significant expansion in the use of renewable sources of energy. In this regard, thoughts are also turning to the use of ammonia as a ‘green fuel’ since it is readily compressed into a liquid, is transportable in bulk and would burn to release harmless water and nitrogen in an exothermic reaction.
4NH3 + 3O2 = 2N2 + 6H2O + HEAT (316.8 kJ per mole of ammonia)
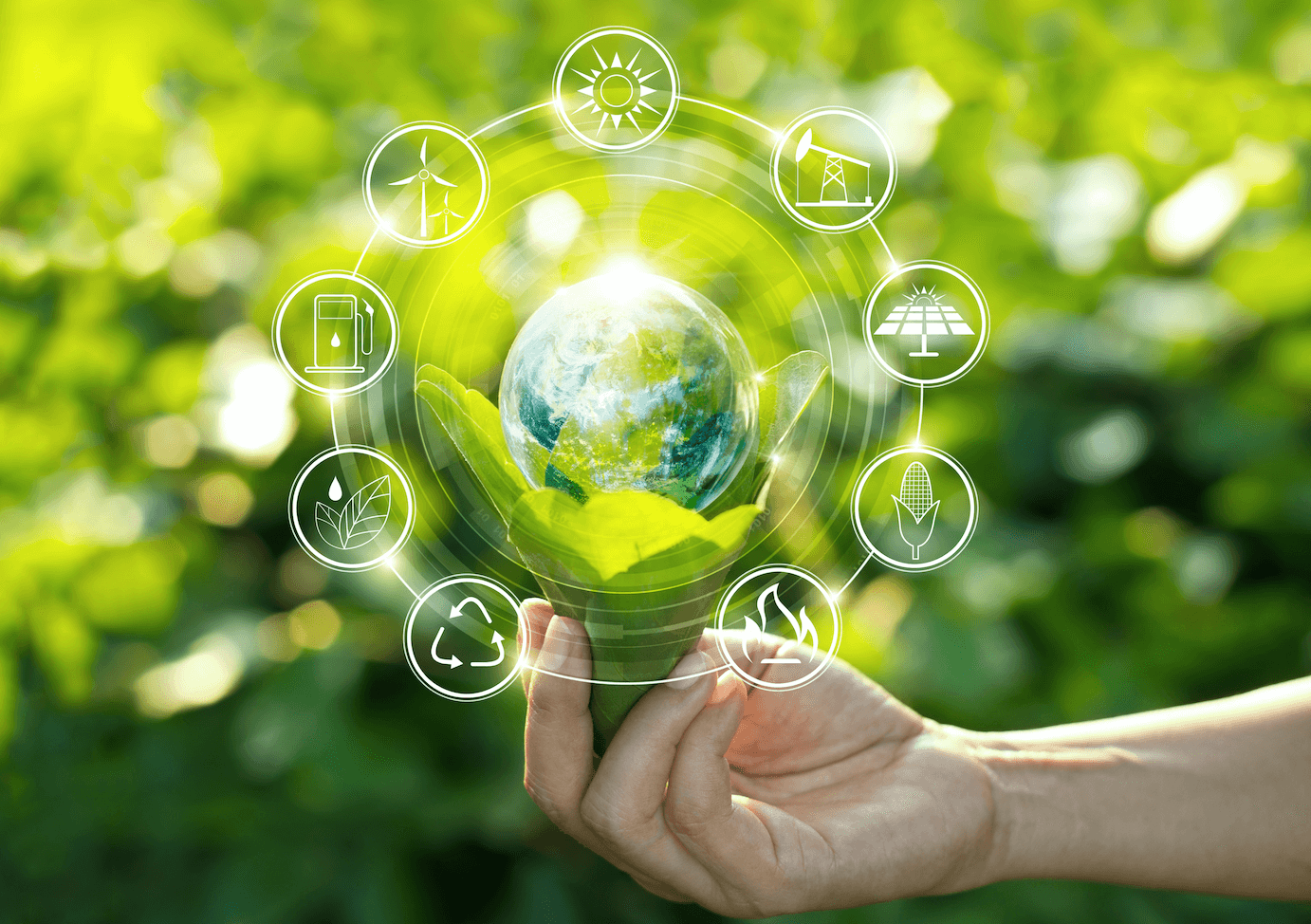
^ Renewable energy sources could include ammonia as a source of green energy
However, consumption of renewable energy by established industry can also make a significant and positive contribution to climate change. Ammonia may be used in this connection as the basis for transporting hydrogen as a source of green energy. Parts of the world rich in reliable solar energy, such as the deserts of the Sahara and central Australia, could provide vast resources of renewable energy to produce inexpensive ammonia which could easily be liquefied and transported to markets in bulk by pipeline and ship tankers. Infrastructure already in existence for the production, storage and bulk distribution of millions of tonnes of ammonia could readily translate into use within an energy economy based on burning hydrogen released from ammonia.
Development and subsequent scale-up of alternative processes in the laboratory in order to produce ammonia in bulk proceed at a very slow pace involving intensive collaboration among specialists working in a number of different fields such as solid-state chemistry, catalysis, electrochemistry and reactor design. Despite persistent research effort and the current high carbon footprint of the energy-expensive Haber Bosch process, it remains, for the present, the basis of the commercially-viable industrial method for maintaining the supply of vitally important ammonia.
References
Marnellos G. Ammonia Synthesis at Atmospheric Pressure. Science. 1998. 282:98–100. Doi: 10.1126/science.282.5386.98
Garagounis, et al. Electrochemical Synthesis of Ammonia: Recent Efforts and Future Outlook. Published in ‘Membranes’ September 2019; 9(9). 112. Doi: 10.3390/membranes9090112
J M McEnaney et al, Energy Environ. Sci., 2017, Doi: 10.1039/c7ee01126a
Department of Business, Energy & Industrial Strategy. UK Energy Statistics, Quarterly Bulletin. June 2020